Commodities
Concord is an active participant in the global markets for non-ferrous metals and associated minerals and raw materials. The products Concord trades, finances, moves and stores are relevant to any number of important global industries ranging from automobiles, aerospace, electronics, construction, consumer products and infrastructure.
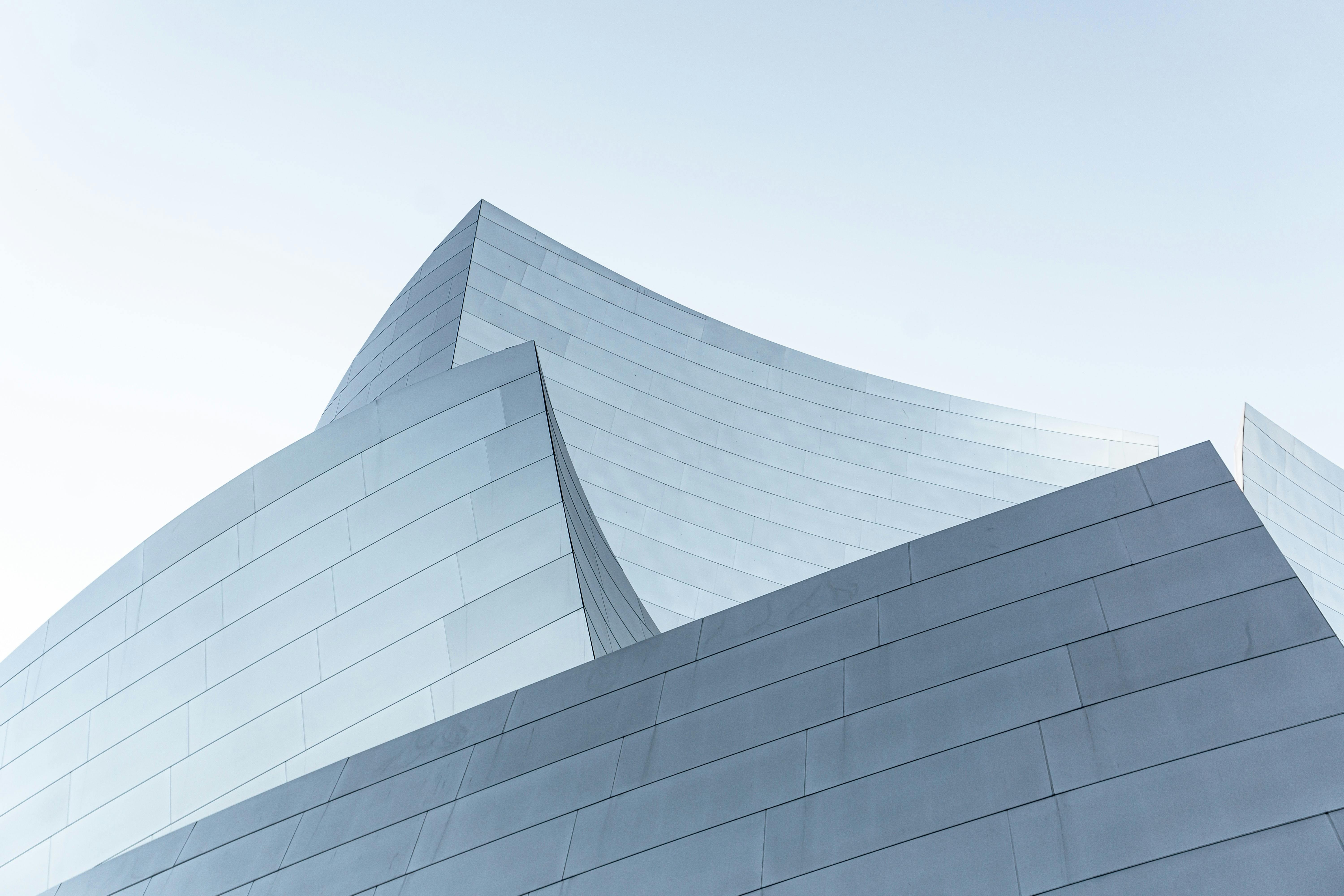
Aluminum
Aluminium is comparatively ‘new’ industrial metal, having been produced in commercial quantities for only a little over 100 years. Yet today aluminium is very widely used in the world around us – if you are visiting Concord’s website today on a computer or handheld device you are using aluminium – and its use is increasing at a faster trend rate than that of any other industrial metal, bar stainless steel. In 2019 the world market for primary aluminium amounted to 64m tonnes, adding more than 50% over the last decade, with a value upwards of USD130bn.
Aluminium is the third most abundant element in the earth’s crust (and more common than iron), providing the resources for production of the metal in many countries around the world. Aluminium is extracted from the raw material, known as alumina, by electrolysis, an energy intensive process in which producers continue to invest to improve efficiency and have succeeded in reducing unit greenhouse gas emissions by over half since the 1990s.
Aluminium’s properties of strength, light weight, ductility, durability, conductivity (of both heat and electricity) and resistance to corrosion make it the material of choice across a wide range of applications, among which building & construction; automotive, aviation & transport; packaging; consumer goods; and power transmission are its main markets. It is aluminium’s light weight (technically high strength-to-weight ratio) especially that brings benefits to its customers. In passenger cars, for example, reducing weight by 10% raises fuel economy by about 7%, with clear environmental and commercial advantages. Aluminium – unlike some competing materials, notably plastics – is also infinitely recyclable, an indispensable attribute in today’s increasingly environmentally conscious world.
WE SUPPLY
- P1020 (99.7%) Ingots, Sows and T-Bars
- High Purity Aluminium Ingots, Sows and T-Bars (P0610, P0406, P0303 etc.)
- Offgrade Aluminium Ingots, Sows and T-Bars
- Billet
- Rod
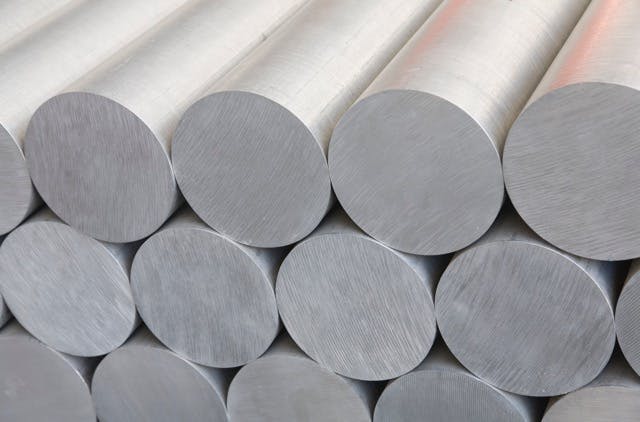
Alumina
Alumina is the everyday name for aluminium oxide – or, more specifically, aluminium (III) oxide (Al2O3), the most common of aluminium’s three oxides. It occurs naturally as the mineral corundum, which in rare circumstances forms the gemstones ruby and sapphire, but most alumina used today is produced artificially for the purpose of making primary aluminium metal, for which ‘metallurgical’ (‘met’) or ‘smelter’ grade alumina is the raw material feed input.
Alumina is extracted from ores known as bauxite and the Bayer process, patented by its inventor, Austrian chemist Carl Josef Bayer, over 140 years ago in 1877, is still today the most commercially successful and widely employed method for refining bauxite to produce alumina. The Bayer process features the following key steps:
1. Milling: bauxite is crushed (to 2-5cm particles, increasing surface area for the digestion step) and washed (to remove silica fines) and then mixed with lime and ‘spent liquor’ (caustic soda returned from the precipitation step) to form a pumpable slurry
2. Digestion: the bauxite slurry is pumped into autoclaves, commonly known in the alumina refining industry as ‘digesters’, in which it is dissolved in a caustic soda (sodium hydroxide) solution at elevated temperature and pressure to yield a solution of supersaturated sodium aluminate, known in the alumina refining industry as ‘pregnant liquor’. Conditions in the digester depend on the mineralogy of the bauxite being processed, of which there are three types. Gibbsite is processed at lower temperature and pressure (±145⁰C, ±5 bar) than boehmite or diaspore (≥250⁰C, ≥38 bar), which requires less expensive equipment and energy input into the process and so ceteris paribus lowers capital and operating costs
3. Clarification / settling: the pregnant liquor is cooled and solid wastes contained allowed to collect at the bottom of settling tanks (sedimentation) from where the resulting residue, known in the alumina refining industry as ‘red mud’, can be more readily removed, before the pregnant liquor is passed on through a series of filters to further reduce impurities
4. Precipitation: the pregnant liquor is then passed on to precipitation tanks where it is progressively cooled, prompting crystals of aluminium hydroxide (Al(OH)3), known in the alumina refining industry as ‘hydrate’, to precipitate out of solution, a process that is accelerated by first seeding the pregnant liquor with the addition of already formed fine crystals returned from the classification step
5. Classification: the hydrate crystals recovered from precipitation are sorted by size using cyclones or gravity classification tanks, and coarse crystals are passed on for calcination while fine crystals are returned to the precipitation step to agglomerate by seeding new crystal formation
6. Calcination: the coarse hydrate coming from the classification step are roasted (or ‘calcined’) at temperatures of up to 1,100⁰C to drive off both free moisture and chemically connected water, yielding an anhydrous white powder that is alumina
It takes about two-to-three tonnes of bauxite to produce one tonne of alumina, depending on the alumina content of the bauxite. In principle, the maximum alumina content of bauxite is 65.4% (pure aluminium hydroxide) but in practice any bauxite containing ≥50% alumina is considered ‘high-grade’ and range as low as ±30% for commercial production of alumina by the Bayer process.
While the bulk of the world’s alumina output (±94%) is used for feed in primary aluminium metal, a small proportion is supplied for other non-metallurgical applications, including abrasives; fillers for plastics; production of chemicals, engineered ceramics, refractories and glass; and in catalysts (most notably for conversion of hydrogen sulphide to elemental sulphur in the refining of crude oil by the Claus process) by virtue of alumina’s properties, including hardness, high melting point and chemical stability.
Today there are alumina refineries operating in 26 countries around the world, and 23 countries producing met-grade alumina. The four largest producer countries – China, Australia, Brazil and India – produce almost 85% of the world’s total alumina output, which is expected to amount to about 133mt in 2020, up +50% in the last decade alone, with a value upwards of USD35bn.
Many alumina refineries, which are typically located close to bauxite mines and / or ports to minimise logistics costs, are owned and operated by producers of primary aluminium metal, although a number produce more alumina than needed for captive feed requirements and the balance is sold into the third-party market, while there are also a small number of alumina refineries operating independently of aluminium smelters. Today the third-party market, on which many non-integrated aluminium smelters depend, accounts for over 40% of the total market for met-grade alumina.
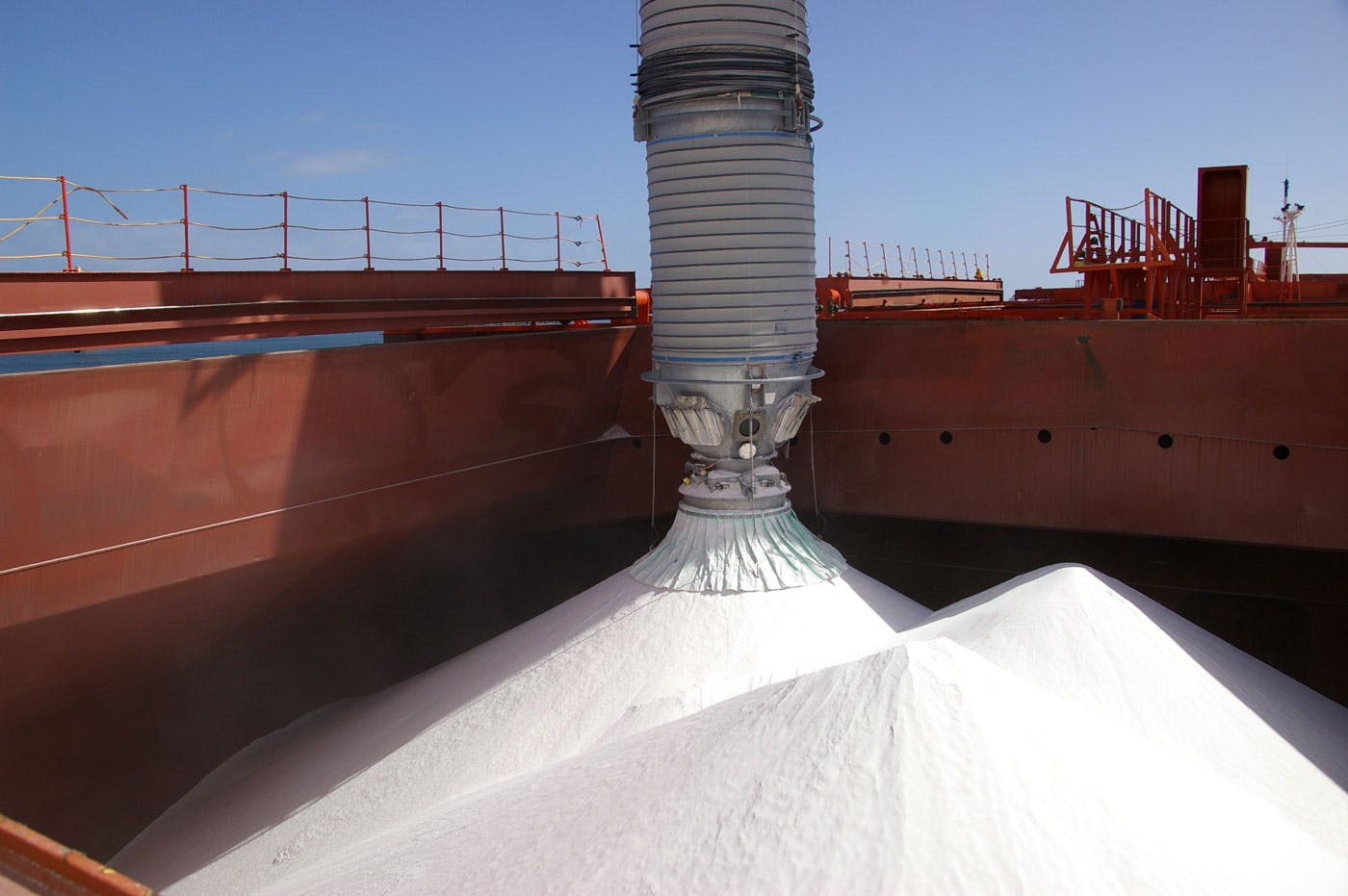
Bauxite
Bauxite is the ore from which most of the world’s primary aluminium metal production is ultimately sourced and takes its name from the village of Les Baux in Provence, southern France, near where in 1821 it was first discovered by the French geologist Pierre Berthe. Bauxite typically contains a mixture of one or more aluminium hydroxide (hydrated alumina) minerals as well as some impurities, which can vary widely, that together determine the conditions under which different types of bauxite are processed and their value. In industrial production of primary aluminium metal, bauxite is first ‘refined’ by a chemical leach process using caustic soda (sodium hydroxide), named after its 19th century inventor Carl Josef Bayer, to produce alumina (aluminium oxide), which in turn is the feed for production of primary aluminium metal by electrolytic reduction of the alumina in a molten bath of natural or synthetic cryolite (sodium hexafluoroaluminate), known as the Hall-Héroult process.
Bauxite, which is typically reddish brown in colour (owing to the presence of iron oxide) and of a dull to earthy lustre, can be classified in different ways: by the geology of the deposit (karst (carbonate) or lateritic (silicate)); the country or region in which it occurs (for example, Jamaican or European); or its intended application (while it is estimated over 85% of bauxite is used to produce alumina, some bauxite has other uses as abrasives or in refractory, cement or chemicals production). Bauxite can also be classified according to its mineralogy, of which there are three types: gibbsite, which contains alumina trihydrate; and the polymorphs boehmite and diaspore, which contain alumina monohydrates. The key difference between the former and the latter is that gibbsite is processed at lower temperature and pressure (±145⁰C, ±5 bar) than boehmite or diaspore (≥250⁰C, ≥38 bar), which requires less expensive equipment and energy input into the refining process and so ceteris paribus lowers capital and operating costs.
Among the impurities invariably occurring in bauxite, by far the most important is silica, which can be present in different forms. Some reactive crystalline forms of silica complicate the alumina refining process, making it more difficult to recover the alumina contained in bauxite, as well as increasing quantities of caustic soda consumed in the refining process to produce alumina. Any mass of silica reacting in the alumina refining process will cause an approximately equal loss of caustic soda and of alumina to red mud residues, the waste product from alumina refining, with the result that reactive silica content is a key element in establishing the commercial value of any bauxite.
Bauxite can also contain potentially valuable by-product metals, which can be accumulated in and recovered from the refining process. For example, bauxite is the main source of gallium, a metal used mainly in the electronics manufacturing industry. However, since the market for gallium is very small, few alumina refineries take steps to recover it.
Most of the world’s bauxite resources occur in tropical, or former tropical, regions where rocks containing aluminium silicates have been subject to intense chemical weathering over many millions of years to yield the ores that are mined today. Bauxite most often occurs in sedimentary layers, typically of 4-6m, at or near surface with little overburden and is usually extracted by open-pit strip mining methods. Today bauxite is mined in 22 countries around the world, of which the four largest – Australia, China, Guinea and Brazil – produce over 80% of a total output expected to amount to about 355mt in 2020, an increase of over 40% in the last decade, with a value (FOB basis) upwards of USD13.5bn. The world’s total bauxite resources are estimated at between 55-75bn tonnes, sufficient to sustain the present rate of primary aluminium metal production far, far into the future.
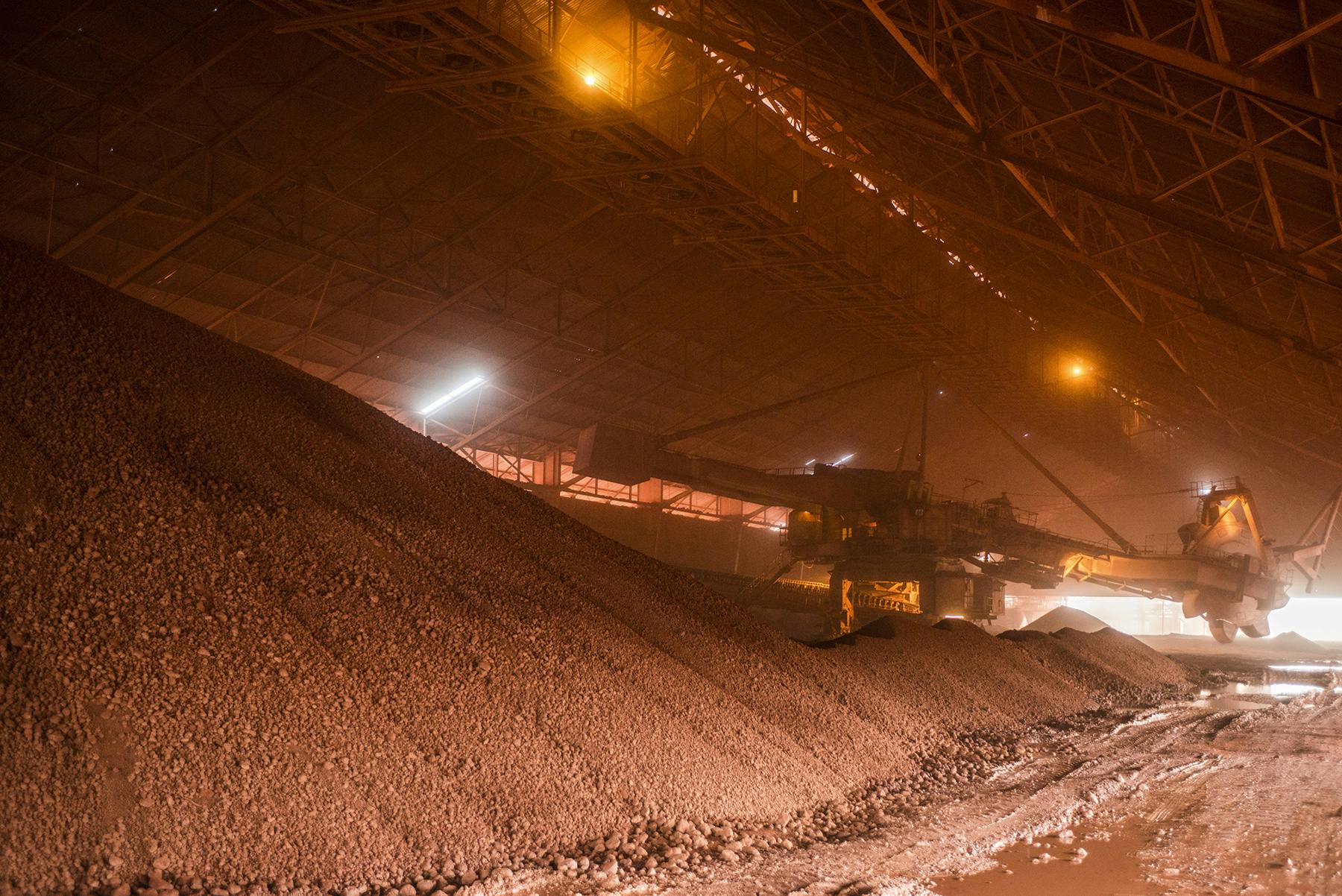
Copper
Copper’s chemical symbol, Cu, comes from the Latin word cuprum, meaning ‘from the island of Cyprus’. It is one of the very first metals to have been used by our ancestors, with archaeological evidence of its discovery dating back about 10,000 years, and the advance that copper alloyed with tin produces bronze brought forward the Bronze Age around 4,500 years ago. Today there are over 400 copper alloys and copper is all around us – if you are visiting Concord’s website on a computer or mobile device you are using copper – as its role in society continues to increase. In 2019 the world market for primary copper amounted to almost 23.5m tonnes, up over 55% since the turn of the millennium, which was worth over USD140bn, making copper the world’s largest non-ferrous metal market by value.
Copper is one of the more common elements in the earth’s crust. Identified resources amount to over 2bn tonnes (metal content), almost two-thirds of which occur in the Americas, and about 40% in South America alone. By contrast, less than 20% occur in Asia, which is now home to over 70% of the world’s primary copper consumption. This mismatch between where copper resources occur and where copper is wanted drives substantial international trade in copper raw materials and metal – refined copper imports amounted to more than 9m tonnes worth over USD55bn in 2019 – that is likely to continue long into the future.
Copper is an excellent conductor of electricity and heat – in fact the best of all non-precious metals – and these attributes along with the ‘red’ metal’s other physical, chemical and aesthetic properties, including ductility, machinability, strength and resistance to creep and corrosion, make it the material of choice in many applications. Copper’s main use is in equipment manufacture – it is essential in energy efficient generators, motors and transformers – followed by building construction, infrastructure and transport. Prospects for future copper demand are very bright looking forward to an increasing number of electric vehicles replacing those driven by oil-fuelled internal combustion engines and expansion of green energy systems. Moreover, recycled copper losses none of its physical or chemical properties and is making a rising contribution to market supply, a quality that is increasingly important in material selection and consumer approval in our more and more environmentally conscious world.
WE SUPPLY
- LME Registered Grade A Cathodes
- Non LME Registered Cathodes
- Offgrade Cathodes
- Blister Blocks/Ingots
- Rod
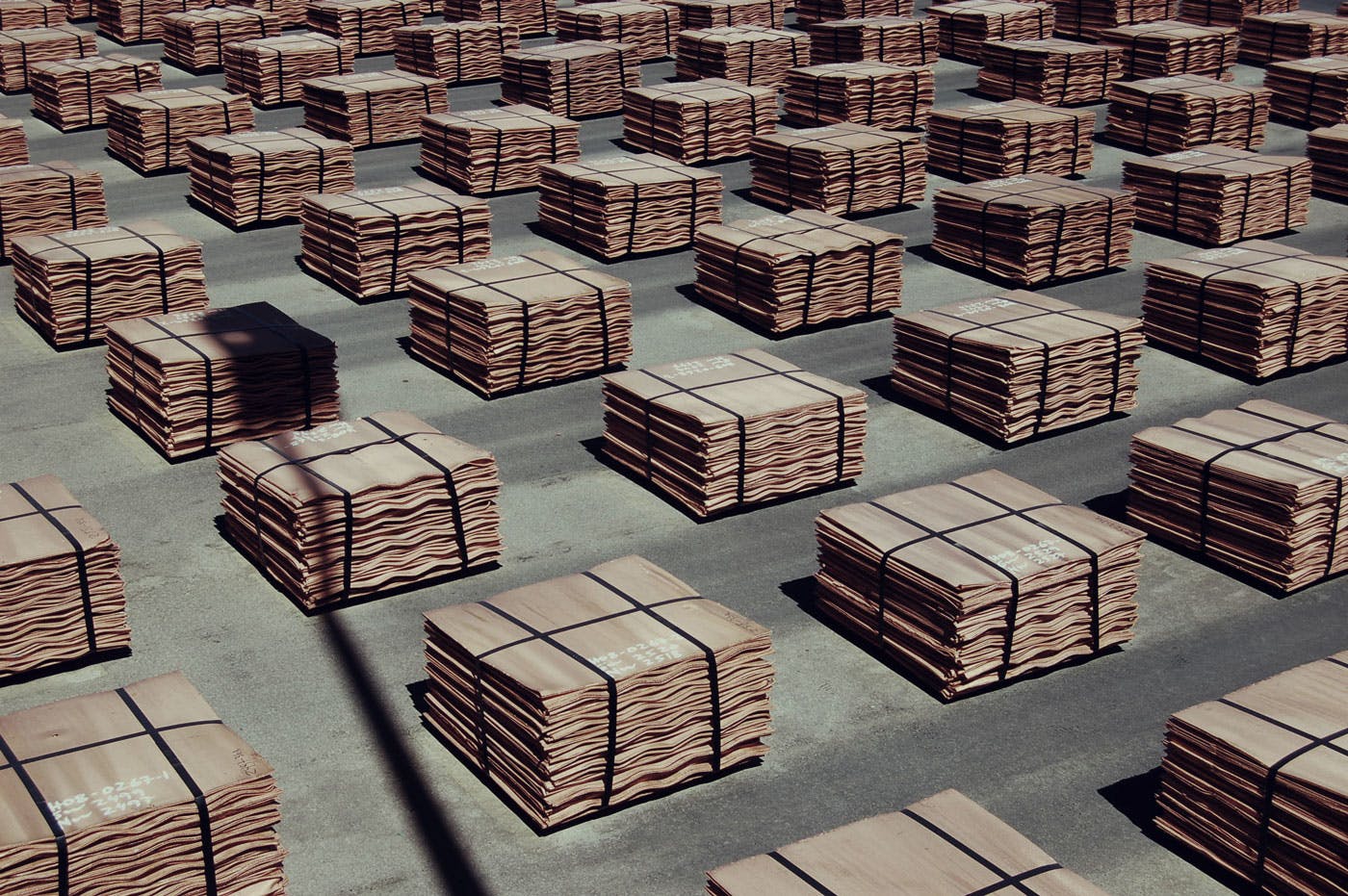
Zinc
Zinc was first isolated and officially identified as an individual element only in 1746, yet its contribution to civilisation stretches back far further in time. Archaeological evidence exists to show zinc metal was already in production around Zawar in northwestern India – an area which is home to some of the largest and richest known zinc deposits to this day – over 500 years earlier, and use of zinc-bearing minerals mixed with copper to produce brass, although without formal understanding, can be traced back thousands of years deep into antiquity. Today zinc is the world’s fourth largest industrial metal market with a value of over USD36bn in 2019 based on output of 13.7mt, which has increased by over half since the turn of the millennium.
Zinc occurs in dozens of different minerals and, since zinc is a chalcophile, sphalerite, a form of zinc sulphide containing about 64% zinc by weight, is the most abundant. Zinc minerals are often found in ores with other metallic minerals, most commonly those of ‘sister metal’ lead as well as silver, which has very important processing and commercial implications. Today the world’s identified zinc resources amount to about 1.9bn tonnes (metal cont), which should be sufficient to meet future demand for many generations to come, and zinc mining is carried out in over 40 countries, led by China, Australia and Peru. Almost all primary zinc metal is now produced by roasting of zinc concentrates to calcines (zinc oxides) that are then leached to yield a solution of zinc sulphate from which zinc metal is recovered by electrolysis in RLE (roasting-leaching-electrowinning) plants that have almost completely replaced the purely pyrometallurgical process by which zinc metal was first produced on an industrial scale.
Zinc’s most important property is probably its capability to protect steel from corrosion, both by providing a physical barrier – the surface of pure zinc oxides quickly with moisture and carbon dioxide naturally in air to form a protective passivating layer of zinc carbonate – and cathodic protection – in the immediate presence of zinc steel will not corrode until all zinc, acting as a ‘sacrificial anode’, has been oxidised. The process of applying zinc to steel to prevent corrosion, galvanising, takes its name from the Italian physician, Luigi Galvani, whose discoveries in 1780s demonstrated the key underlying principles. Today galvanising accounts over 50% of total zinc metal use, serving a very valuable purpose by reducing the lifecycle costs and lightening the environmental footprint of steel used in construction, cars including electric vehicles, and many other applications. About another one-third of zinc metal is used in making brass and a range of die-cast alloys, mainly with aluminium, products that in their turn are also widely used in construction and car making. Much of the balance of zinc metal is used to synthesise zinc chemicals, which in their turn are ingredients in myriad products from fertilisers to sunscreens, and directly in the form of zinc sheet for use in buildings and perhaps seen in the skyline of central Paris.
WE SUPPLY
- Special High Grade (99.995%) Ingots and Jumbos
- Ingots and Jumbos (1/1.5MT per Piece)
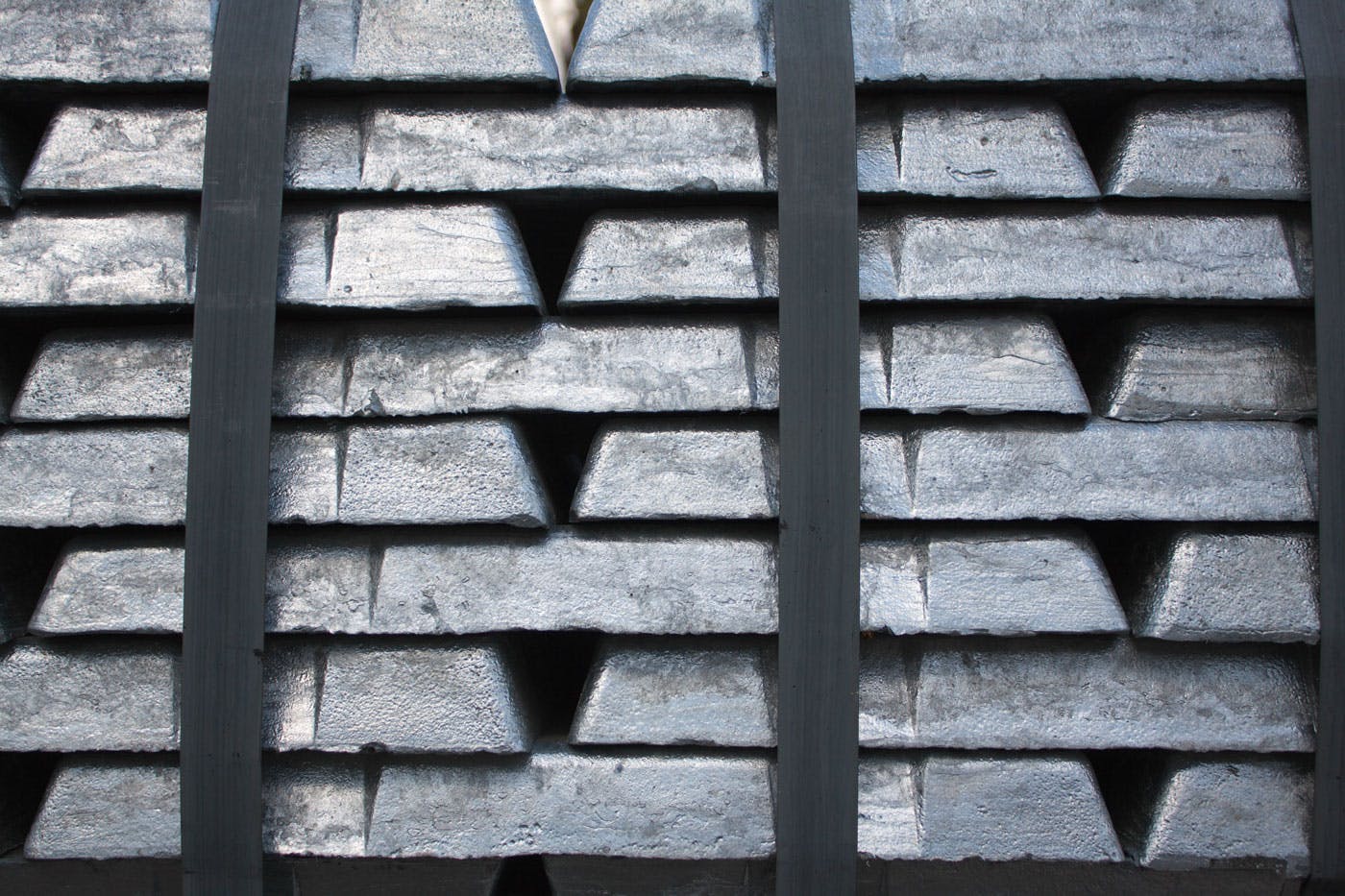
Nickel
Nickel derives its name from a German word for one of its rarer ores, reddish-brown in colour, first unearthed in the Erzgebrige (Ore Mountains) of Saxony in the southeast of the country in the 1600s. ‘Kupfernickel’, meaning devil’s copper and now known as nickeline, was so-called because it was originally but wrongly thought to contain copper yet did not yield the red metal on smelting. It was not until over a century later, in 1751, that nickel was first isolated and identified as an individual element by Swedish chemist Alex Cronstedt. Since very few nickel resources were then known, however, nickel was subsequently little used, and it was not until the mid-to-late 1800s following the discovery of large nickel-rich ore bodies in Scandinavia, New Caledonia and Canada that common commercial use of nickel began. Today nickel is the world’s fifth largest industrial metal market with a value of USD34.6bn in 2019 based on an output of 2.4mt, which has more than doubled since 2000.
Nickel occurs in about 50 different minerals and identified land-based resources averaging at least 1% nickel amount to about 130mt. Most of these present in ore deposits of two main types: sulphide ore bodies of igneous origin principally featuring the mineral pentlandite, which typically occur at depth and commonly also include cobalt, copper and / or precious metals (gold and / or PGMs), today accounting for about 30% of resources; and laterite ore bodies, which are typically larger but of lower grade, arising from prolonged physical and chemical weathering of igneous rocks in present or past tropical regions and occurring at or near surface, today accounting for about 70% of resources. Until recent decades sulphide ore bodies supplied feed for the majority of nickel production, despite making up the smaller share of resources, since processing of sulphide ores was generally less complex and lower cost. Today the share of nickel laterites in total metal production has increased to about 70% as processing technology and finished nickel products have evolved. Nickel is now mined in over 25 countries around the world, of which Indonesia (nickel laterites) has the highest output, followed by the Philippines (nickel laterites), Russia (nickel sulphides), New Caledonia (nickel laterites) and Canada (nickel sulphides).
There is no standard approach to production of primary nickel, which is not one single product but a group of products of different metallurgies and physical forms – only about 40% of world output is refined nickel metal of specification (≥99.8% nickel) and form (briquettes, cathodes, pellets) that could be delivered to physically settle the LME-traded contracts that set benchmark prices globally. Over 55% of nickel is produced in the form of iron-nickel alloys, known as ‘ferronickel’ (FeNi), although this itself is not a standardised product and nickel content varies widely. Over two-thirds of world ferronickel output is referred to as “nickel pig iron” (NPI). Produced in Indonesia and China, NPI is simply an iron-nickel alloy, although the nickel content is typically less than the 15% minimum the ISO designates for describing a product as ferronickel.
Nickel has a number of valuable properties that it brings to the applications in which it used. Nickel alloys very readily with other metals, it is strongly resistant to corrosion and oxidation, highly ductile, strong and tough, and these properties hold even at high temperatures. Today nickel’s main use is in making stainless steels (iron-chromium alloys) in which it imparts increased formability, strength, toughness and resistance to corrosion and heat, accounting for over two-thirds of primary nickel consumption on a first use basis in the form of FeNi / NPI plus some refined metal, up from only one-third in the last three decades. (Note, however, not all stainless steels contain nickel and it is chromium (minimum 10.5% by weight), not nickel, that makes steel ‘stainless’.) Stainless steels, in turn, are used in myriad applications in commercial and home appliances; energy and heavy industry; automotive and transport; and architecture and construction, and output has been rising at a faster rate (about 5.5% pa) since the turn of the millennium than for any other industrial metal, reaching a new record of over 53mt in 2019, of which almost 80% were so-called ‘austenitic’ (i.e. nickel-bearing) stainless steels. Another 15% of primary nickel is used in producing other ferrous and non-ferrous alloys (notably with copper), 7% for electroplating of metal goods, and a small but with the accelerating uptake of electric vehicles now rapidly rising amount of primary nickel is used in making rechargeable batteries, in which nickel increases energy density and storage capacity.
WE SUPPLY
- Primary Nickel (99.80%)
- Briquettes
- Full Plate Cathodes
- Cut Cathodes (4×4, 2×2, 1×1)
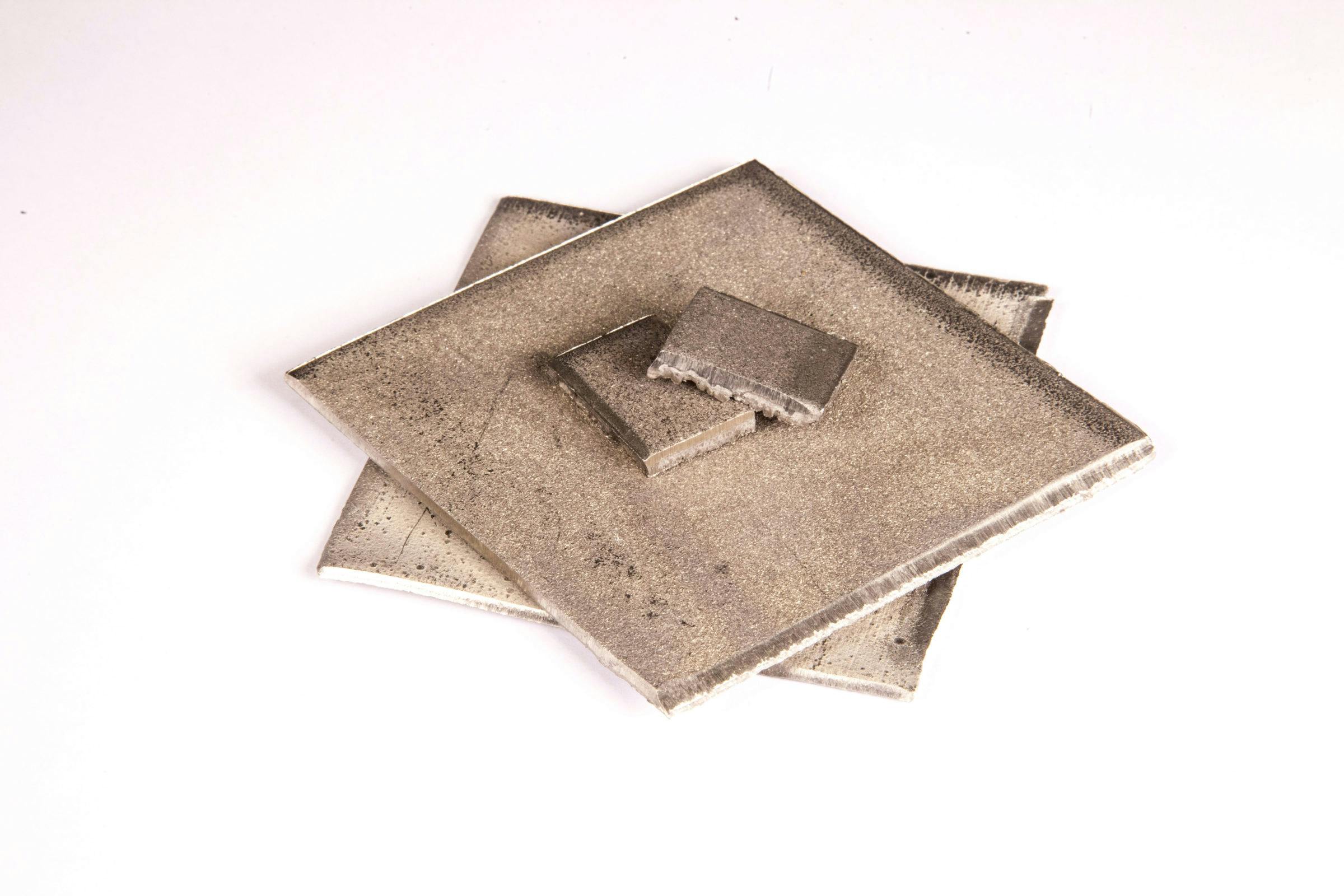
Cobalt
Cobalt-based blue pigments, now known as ‘cobalt blue’, have been used since ancient times in jewellery and to colour ceramics, glazes and glass. In Medieval times, cobalt-bearing ore occurring in the Schneeberg Mountains of what is today southeastern Germany and lower Austria was nicknamed ‘kobold’ (meaning goblin) on account that when smelted using the techniques of the time it yielded little metal but instead hazardous arsenic fumes. It was only some hundreds of years later that Swedish chemist, Georg Brandt, experimenting to understand the nature of ‘cobalt blue’ colouring in glass, demonstrated in the late 1730s that kobold ores could be reduced to a new metal, the first to be discovered since antiquity. Subsequently, the studies of the US metallurgist Elwood Hynes in the early 1900s made the discoveries that inform many of the uses that cobalt has today.
Cobalt is not very rare, ranking in the upper one-third of occurrence rates of all known elements in the earth’s crust. There are around 30 principal cobalt-bearing minerals, mostly sulphides with other base metals, and over 100 more contain cobalt in minor amounts. However, cobalt arises in recoverable concentrations less commonly across a limited number of countries, with world total resources today estimated at about 7mt (metal contained), of which about half is found in the Democratic Republic of Congo (DRC), and it is for this reason coupled with prospects for cobalt’s future use that it is now frequently referred to as a ‘critical’ raw material.
Cobalt today is mined in 19 countries, mainly as a by- or co-product in copper or nickel mining operations, which has important implications for cobalt supply and price dynamics. By far the largest cobalt mine output comes from the DRC, supplying over 70% of the world total in 2019, and the top four cobalt mining countries, also including Australia, the Philippines and Cuba, supplied over 80% of the total. Most cobalt-bearing raw materials recovered from mining operations are subsequently processed to produce cobalt chemicals or refined metal. The majority of these processors (~75% in 2019) are not integrated with mining operations and purchase raw material feed from third parties.
The world’s total output of refined cobalt (chemicals and metal) amounted to about 140,000 tonnes in 2019, up 85% over the last decade, with a value approaching USD5bn. Only six countries produced cobalt chemicals, of which China was by far the largest with output of almost 79,000 tonnes out of a world total of around 95,000 tonnes, followed at a distance by Finland with around 16,000 tonnes. 11 countries produced cobalt metal in various forms – briquettes, cut and broken cathodes, ingots, powders and rounds – of which China was again the largest with about 7,500 tonnes out of a world total of almost 35,000 tonnes, and China was the only country to produce both cobalt chemicals and metal.
Cobalt has many applications which depend on its specific properties. Cobalt metal is hard, strong and tough, resilient to heat with a very high melting point, resistant also to wear and corrosion, and ductile, although only moderately malleable. Cobalt is also one of only three naturally magnetic metals (the other two are iron and nickel, which sit either side of cobalt in the periodic table). While cobalt can be substituted in some of its applications this may result in reduced performance and / or increased cost.
Today about two-thirds of the cobalt market is for its chemicals, a share which is on a rising trend, and about one-third for refined metal. Among cobalt chemicals, cobalt oxide is the most widely used, today accounting for over 50% of total chemicals demand in terms of cobalt content, followed by cobalt sulphate, accounting for almost one-third of the total. Cobalt oxide is used mainly in the manufacture of lithium-cobalt-oxide (LCO) batteries for electronic goods, such as smartphones, laptops and tablets. Cobalt sulphate is used mainly in making lithium-nickel-manganese-cobalt (NMC) and lithium-nickel-cobalt-aluminium oxide (NCA) batteries, in which it increases energy density and acts as a cathode stabiliser, for electric vehicles and some portable electrical devices. Cobalt chemicals are also used as catalysts in the petroleum and chemicals processing industries, dyes and pigments, drying agents for paints, manufacture of tyres and to generate gas for the inflation of airbags in cars.
The main use of cobalt metal is in the manufacture of so-called ‘superalloys’, today accounting for about 45% of the total metal market, that in turn go into the manufacture of gas turbines and jet engines, for which cobalt’s ability to retain mechanical strength at high temperatures and its wear resistance are critical properties. Cobalt metal is also used in making cemented carbides, also known as ‘hardmetals’, that in turn are used to machine component parts across a range of manufacturing activities, including automotive, shipbuilding, steel fabrication and information technology, accounting for about one-quarter of the metal market, and in magnets for a very wide range of applications, accounting for upwards of another 10% of the metal market.
The market for cobalt is fast changing, however, not least because its key applications are involved in a number of new and evolving technologies. It is widely forecast that demand for cobalt will increase substantially in future, driven in particular by the transition of the world’s motor vehicle fleet from internal combustion engines to battery-powered electric vehicles, in which is expected cobalt will remain a critical element.
WE SUPPLY
- Cathodes (Cut)
- Cathodes (Broken)
- Ingots
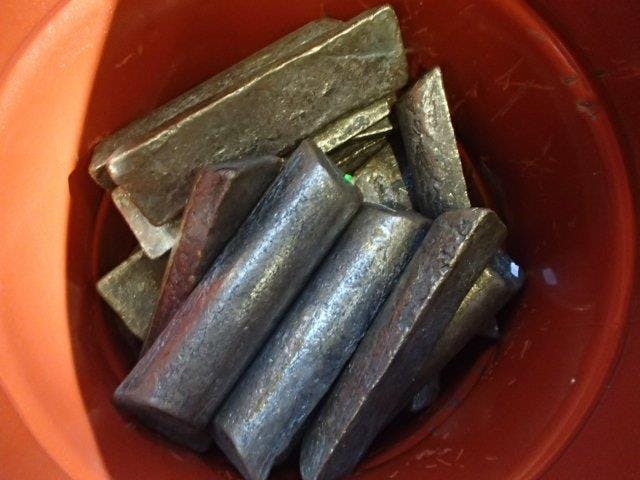
Lead
Lead, one of the seven ‘metals of antiquity’ and deriving its modern name from an old Saxon word meaning metal, has been known to humanity for millennia. In the Roman world, lead was widely and vitally used for water pipes; in the production of pewter (an alloy of tin with lead) for a range of metal goods; and in paints, owing to the very good white covering qualities of lead oxide, and lead metal was being produced on a scale that would not be seen again until the industrial revolution starting in the 1760s. Today lead is the world’s sixth largest industrial metal market with a value of over USD25bn in 2019 based on an output of 11.9mt – which, perhaps surprisingly to some, has increased by almost 80% since the turn of the millennium.
Lead occurs in over 100 different minerals, the most common of which is galena (lead sulphide) and many others are related to this. Lead minerals are often found in ores with other metallic minerals, most often those of ‘sister metal’ zinc as well as silver, gold and copper, which has very important processing and commercial implications. Identified lead resources amount to over 2bn tonnes (metal cont) and lead is mined in about 35 countries around the world, of which China has the highest output, followed by Australia and Peru. Primary lead metal (meaning metal originating from newly mined ore) is produced by pyrometallurgical processing of lead concentrates to yield crude lead ‘bullion’, which is then further refined to remove remaining contaminants and arrive at the final high-purity lead metal product.
Today, however, the majority of lead metal is produced by recycling of lead scrap, recovered mainly from expired lead-acid batteries through one of the most successful closed-loop recycling systems yet established – it is estimated recycling of lead-acid batteries now exceeds 95% worldwide, and in some countries 99% – an indispensable attribute in a world increasingly aware of the need to manage natural resources sustainably. Secondary lead output (meaning metal produced from scrap) provided about 65% of the world’s total lead metal production in 2019, up from less than 55% in 2000 and by far the largest proportion of output of any industrial metal.
Lead metal has many useful properties which have shaped how it is used. Lead is the softest of the industrial metals – which can be well understood when you consider that room temperature (20°C, 293K) is already almost half-way to lead’s low melting point (600.6K, 327.5°C) – and highly malleable, so easy to shape and roll into sheets. Lead is also strongly resistant to corrosion and, with the highest atomic number of any stable (non-radioactive) element, lead has a higher density than most common materials. However, it has also been known since the late 1800s that in some circumstances lead can be harmful to human health – if, for example, released into air or water – and some former applications have been discontinued accordingly.
Today, lead’s main use, one with which most of us are familiar and accounting for over 85% of its market, is in production of lead-acid batteries for motor vehicles to start the engine and provide power for electrical equipment (including in electric vehicles); other motive applications from underground mining equipment to golf carts to electric bikes in China, which have added much of the new demand for lead since the early 2000s; and stationary / back-up power in UIP systems serving critical and strategic infrastructure from hospitals to telecoms networks and data centres, as well as load levelling and renewable energy storage systems for electric utility companies. Smaller amounts of lead are still used in a number of other applications, foremost among these pigments and chemicals; rolled products for construction and the chemical industry; ammunition; alloys including certain solders; cable sheathing; radiation shielding; and weights of various kinds – in 1993 around 600 tonnes of lead was used to stabilise the famous Leaning Tower of Pisa in Italy.
WE SUPPLY
Ingots

Talk to us for further information regarding our available Commodities
If you have any further questions regarding Concords availaible comodities services and how we can partner to support your needs.r